Dry-Ice Blasting for Mold Remediation
The most successful and consistent method
for mold remediation is Dry Ice Blasting. Unlike other media
in a blast stream, dry ice does not damage or wear on
plumbing or electrical, is fully adjustable in aggression.
But usage of dry ice blasting is limited. Dry ice blasting
is not very effective at removing dark mold staining on
wood. For removing dark mold staining especially on attic
ceilings we have other products that work better than dry
ice blasting.
Dry-ice is Safe on Electrical |
Dry Ice Blasting is a non-conductor of
electricity, so live electrical equipment and wiring
does not have to be removed or de-energized during
the remediation process. Dry Ice Blasting
leaves a dry surface, eliminating the need for
drying downtime and making it safe on electrical
components and wiring, junction boxes, power panels,
ductwork, and plumbing. Motors, control panels and
electrical equipment are safe from short circuiting
or equipment damage that is associated with any
other cleaning method.
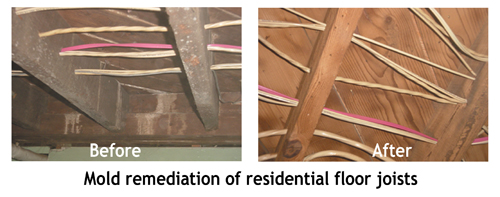
|
Dry-Ice Blasting Before & After Pictures
on a 7/2019 attic mold remediation job
this attic ceiling had a high level of aspergillus mold
growth
Attic Ceiling Mold Removal - Before
Pictures
(click to expand)
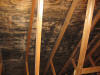
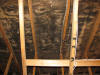
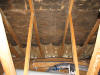
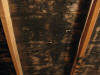
Attic Ceiling Mold Removal - After
Pictures (same attic)
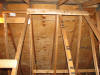
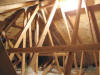
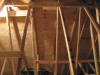
Dry-Ice Blasting - How it Works
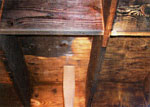
Dry ice blasting for mold remediation
uses four physical properties of air-propelled dry ice
pellets: velocity, abrasion, thermal shock, and evaporation. Dry ice is
solid (frozen) carbon dioxide. For blasting uses, dry ice is
manufactured in pellets of various sizes appropriate to the
substrate to be cleaned. The pellets are hurled from a
blasting gun by air pressure, which provides the velocity.
When the pellets strike the surface to be cleaned, three
things happen. First the velocity of the pellet strikes the
substance to be removed. Because dry ice is at a temperature
of -109 degrees F., the thermal shock helps loosen and lift
the substance to be removed. Finally, the dry ice pellet
flashes into carbon dioxide gas, providing more lift to the
substance to be removed. The carbon dioxide gas is harmless,
leaving no cleaning material such as sand or solvents to be
cleaned up after the cleanup.
Complete mold removal and remediation
requires solving the moisture problem that enabled the mold
to grow in the first place. A mold needs food, such as wood;
moisture; and a temperature range favorable to the growth of
the specific mold organism. Grinding, sanding, or
wire-brushing to remove mold growth does not sanitize the
surface and kill the mold spores. Without dry-ice blast
cleaning, a biocide/sanitizer/cleaner is needed to kill the
mold spores. Dry ice blasting will almost rid the need for
biocides and thus, enhance occupant
and worker safety. Its a great option for mold remediation
in areas with a chemical sensitive individual.
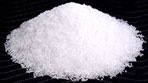
high density dry-ice pellets
Dry-Ice-Blasting - Technical Information
Pellet Kinetic Energy
The
dry-ice blasting process incorporates high velocity
(supersonic) nozzles for surface preparation and coating
removal applications. Since kinetic impact force is a
product of the pellet mass and velocity over time.Even at
high impact velocities and direct head-on impact angles, the
kinetic effect of solid CO2 pellets is minimal when compared
to other media (grit, sand, PMB). This is due to the
relative softness of a solid CO2, which is not as dense and
hard, as other projectile media. This characteristic is a
plus. This prevents damage to the wood surfaces and
electrical wiring. Also, the pellet changes phase from a
solid to a gas almost instantaneously upon impact, which
effectively provides an almost nonexistent coefficient of
restitution in the impact equation. Very little impact
energy is transferred into the coating or substrate, so the
blasting process is considered to be nonabrasive.
Thermal Shock Effect
Instantaneous sublimation (phase change
from solid to gas) of CO2 pellet upon impact absorbs maximum
heat from the very thin top layer of surface coating or
contaminant. The very rapid transfer of heat into the pellet
from the coating top layer creates an extremely large
temperature differential between successive micro-layers
within the coating. This sharp thermal gradient produces
localized high shear stresses between the micro-layers. The
high shear produced over a very brief expanse of time causes
rapid micro-crack propagation between the layers leading to
coating final bond failure at the surface of the substrate.
Thermal-Kinetic Effect
The
combined impact energy dissipation and extremely rapid heat
transfer between the pellet and the surface cause
instantaneous sublimation of the solid CO2 into gas. The gas
expands to nearly 800 times the volume of the pellet in a
few milliseconds in what is effectively a "Micro-explosion"
at the point of impact.
The
"Micro-explosion," as the pellet changes to gas, is further
enhanced for lifting thermally-fractured coating particles
from the substrate. This is because of the pellet's lack of
rebound energy, which tends to distribute its mass along the
surface during the impact. The CO2 gas expands outward along
the surface and its resulting "explosion shock front"
effectively provides an area of high pressure focused
between the surface and the thermally fractured coating
particles. This results in a very efficient lifting force to
carry the particles away from the surface.